Motivation
The project aims at testing Oil-Free Lubricants under industrial conditions for the cold rolling of packaging steels and steels for the automotive industry, and at demonstrating the subsequent processability of the rolled steels down to the coated final product.
The lubricant in the cold rolling process must fulfil high requirements regarding its functional properties, (e.g. cooling, lubrication, and cleaning), as they strongly affect productivity, the process stability and the product quality. Moreover, compatibility with subsequent processes and requirements arising from the final use cases is of high importance.
Commonly, conventional oil-based lubricants (emulsions) are used in the rolling processes. During the rolling process, this emulsion gets contaminated with wear particles and tramp oils. Sludge (wear particles with deteriorated / cracked oils) accumulates in the tank system and the filtration / skimming processes might become inefficient. Production losses due to the fluctuations of the emulsion conditions can also arise.
To sum up, the high effort in maintenance and care and insufficient product quality calls for alternatives.
In a previous project named RollOilFree, oil-free lubricants (OFLs) were developed to replace conventional oil-based lubricants in steel cold rolling. RollOilFree II targets successful transfer of OFLs into the industrial standard of steel industry to help evolution of steel industry towards a greener production.
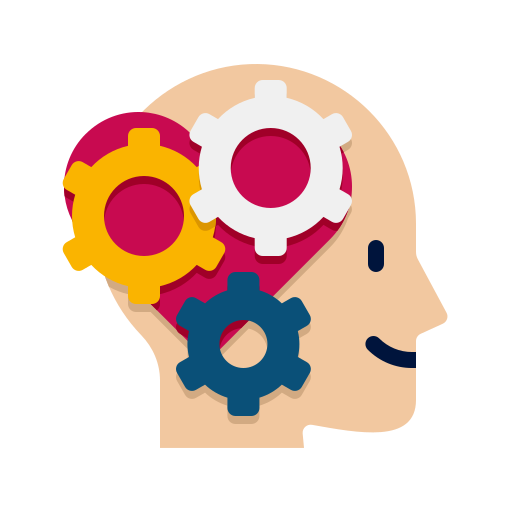
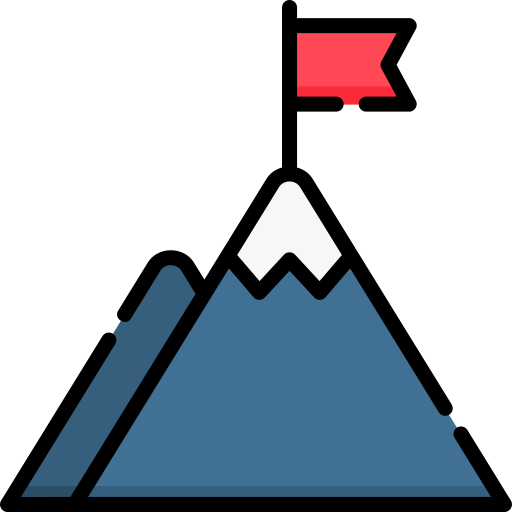
Mission
The substitution of oil/water lubrications by oil-free lubrications (OFLs) has become increasingly important for next generation technologies in the hot and cold forming areas. Beside mere technical functions these lubricants can help fulfilling societal demands of environmentally friendliness / biodegradability and overall sustainability. In the steel sector, OFLs were investigated mostly at laboratory small-scale trials, but a deficit still exists in their further optimisation and adaptation under industrial conditions to be able to capture the specific conditions of the industrial practice of cold rolling steel. This requires for a testing of the OFLs under industrial conditions possible on pilot scale and then on industrial level.
RollOilFree II, as a Pilot and Demonstration project, aims at providing feasible concepts for the transfer of OFLs into steel cold rolling as a new industrial standard, with a focus on two use-cases: automotive and packaging steels, which present high requirements. For instance, packaging steels require high stability at thin gauges combined with a good formability for can making. The most important requirement for automotive steels is superior surface quality and high mechanical strength with nevertheless good workability and excellent coating quality.
Furthermore, RollOilFree II goes beyond testing the lubrication performance in the rolling process, by providing easy manageable solutions for the complete peripheral processes for the use of OFLs (care, maintenance, monitoring, etc.). Finally, to grant an easy transfer into industrial practise and thereby become the new standard for greener steel production, a feasibility study will be done to enable easy, trouble-free and widespread adaption in the European cold rolling industry.
Methods
The methodology implemented in the project is composed of the following steps, all contributing to the evaluation of Oil Free Lubricants (OFLs) as future industrial standard for steel cold rolling:
To sum up, three adaptation and improvement stages for OFLs are foreseen, according to the following scheme
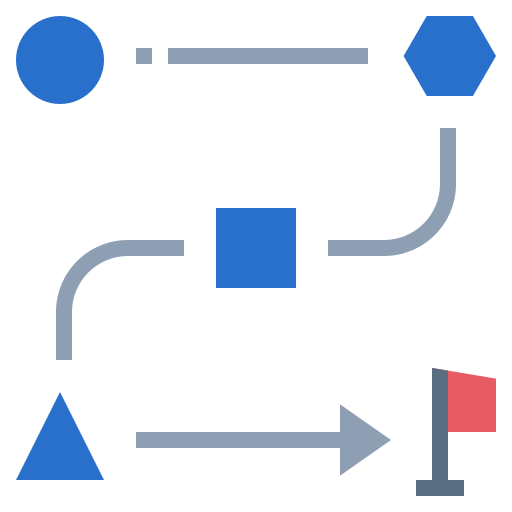
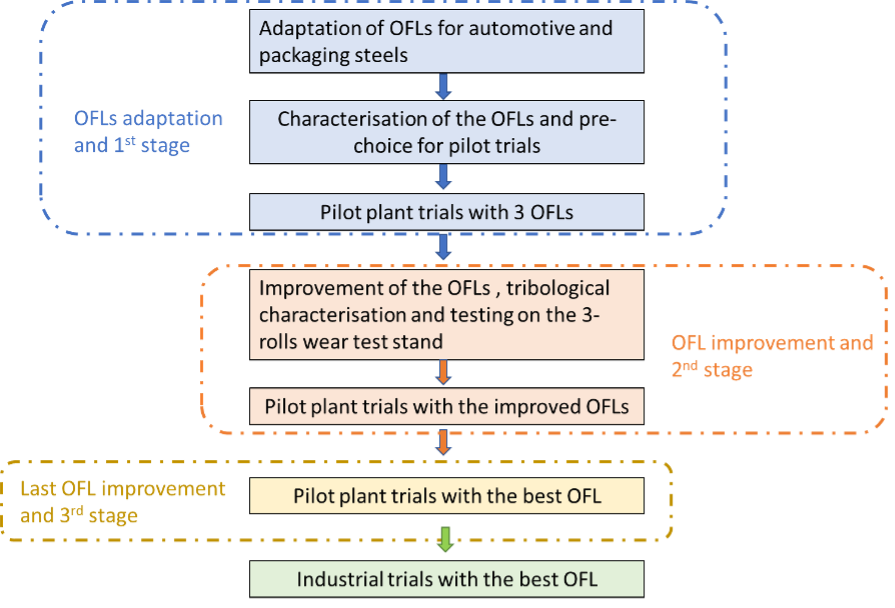
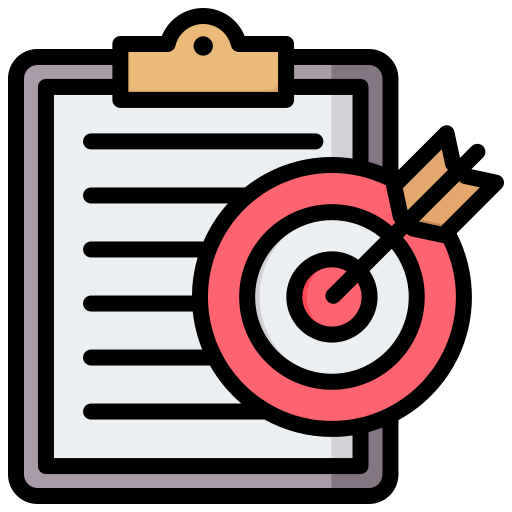